First off. Wow, sorry it took so long to get this next step on the blog. Cold weather and life have kept me away from the shop more than usual since my last post. Meanwhile my faithful reader(s?) has been waiting for a conclusion to this project. Fear not. The conclusion follows.
Interestingly enough, the last issue of the AAW magazine hosted an article specifically to turning finials. There are also several YouTube videos that have great detail about turning finials also. Hopefully Ill add videos to my posts some day, but till then youll just have to read along.
I am using Ebony for the finials in this project. I think the Bradford Pear globe and the Ebony finials will make a great combination. Ive worked with Ebony a fair amount in guitar building, but have never turned it. I was happily surprised with how well it behaves on the lathe.
Instead of using a piece of 1.5" square material to make the finials, I segmented the construction. Since Ebony is expensive, I opted to conserve as much material as possible. The two flat squares (1.5"x1.5"x.5") pictured below will be the "collars" and the rectangular piece (1"x1"x4") will be the finial.
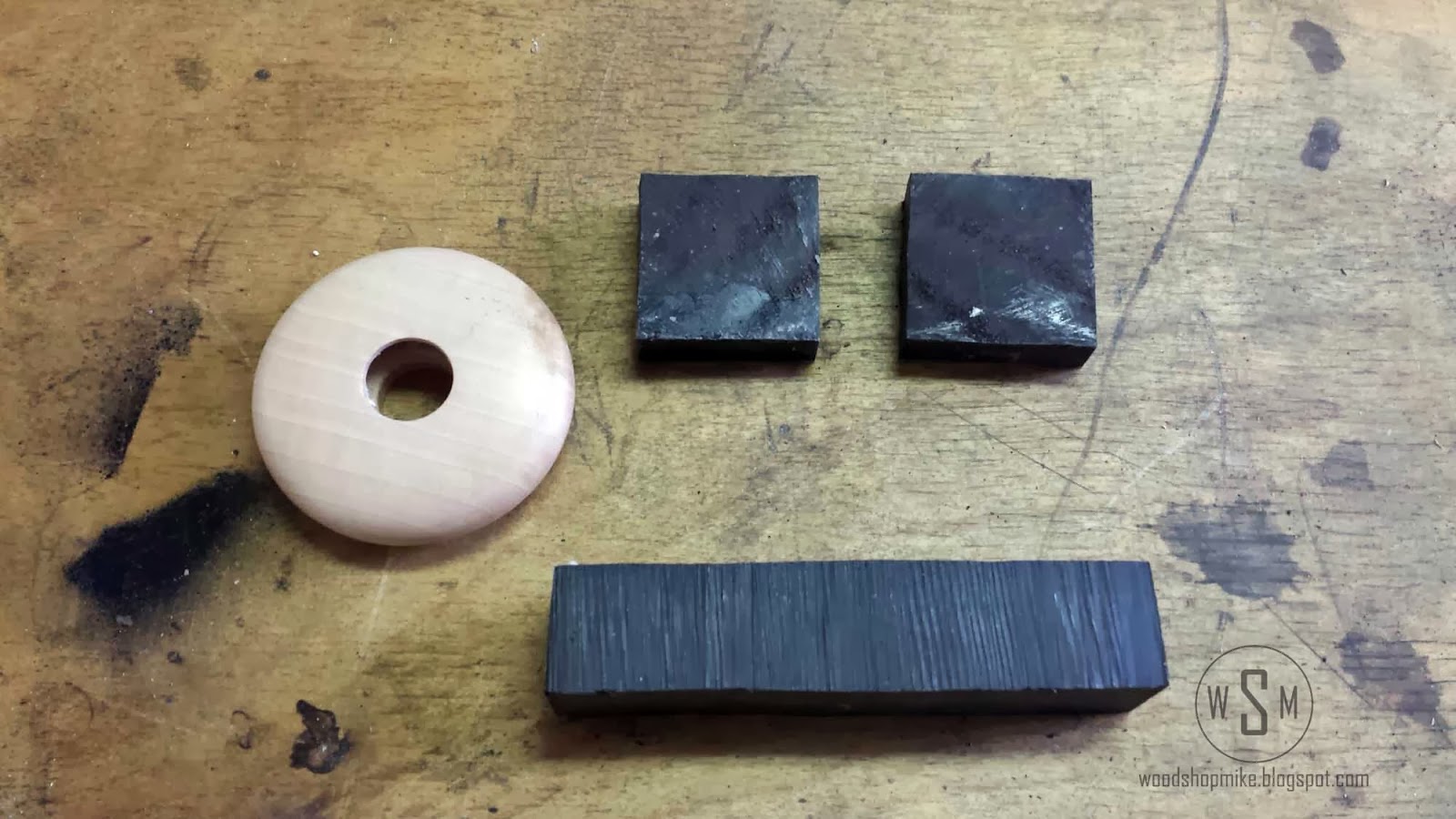
To turn the collars, I start by friction driving the piece between the chuck and the tailstock. As you can see, the jaws of the chuck are fully closed and the piece of Ebony is only being driven with friction. Now, before you just willy nilly toss your piece on the lathe, you need to create a flat surface on the side that sits against the chuck jaws. I accomplished this with a large stationary sanding block that recesses into my workbench. You need to make the piece flat enough to create adequate surface contact and prevent the piece from rocking off the surface of the jaws. Once thats done, just sandwich the piece between the jaws and tailstock. The jaws Im using are the Nova pin jaws.

Light cuts are in order here. If you take too heavy of a cut the jaws will just spin on the flat surface youve created. Once you ease up on the pressure, the piece will start spinning again. The objective of this step is to create a tennon that will recess into the globe. This tennon is also used as a chucking point to shape the outward facing surface of the collar.
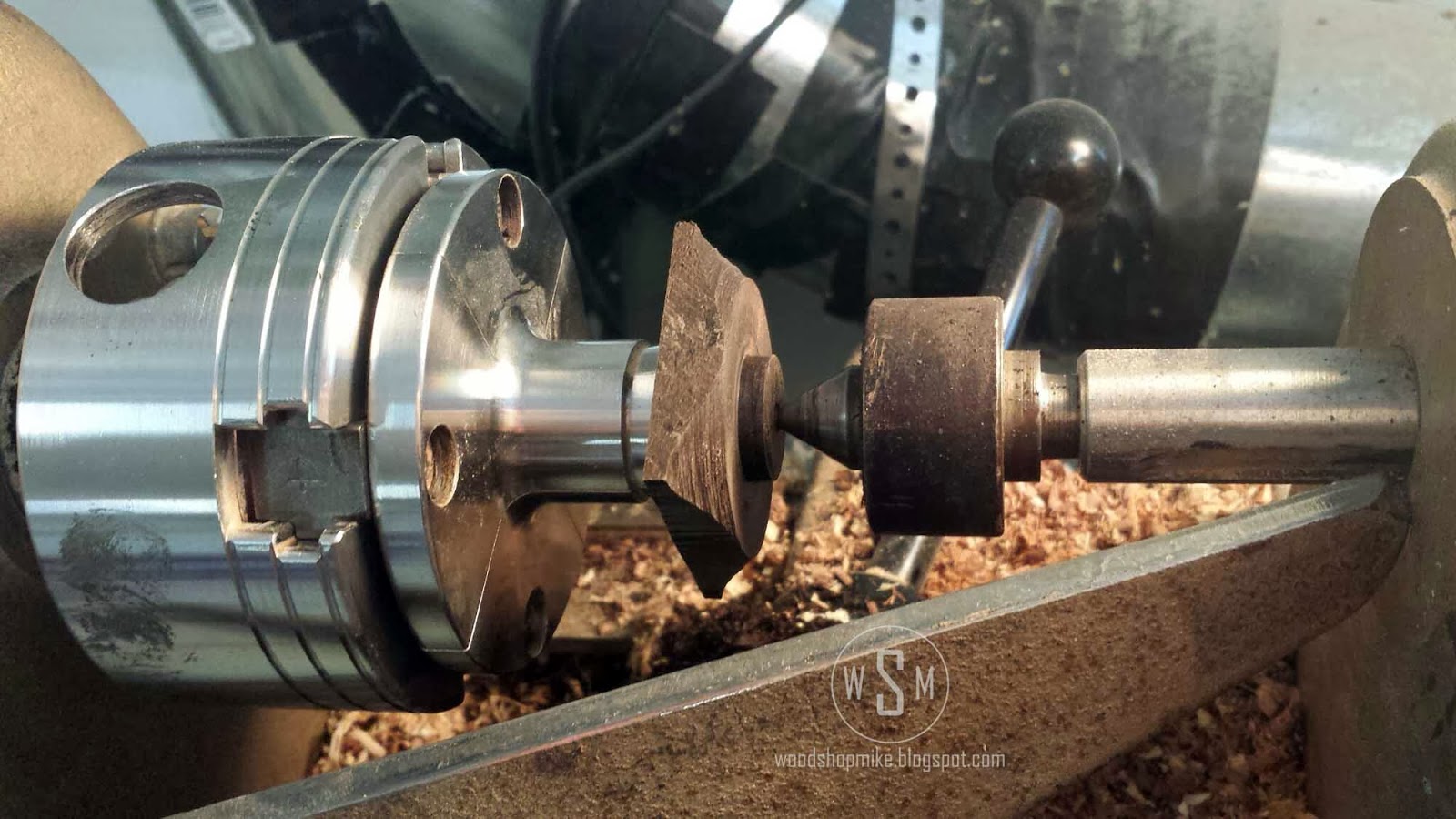
With the collar reversed, you can create your design and drill a center hole for the finial to locate into. This is also the time for sanding and finishing. I sand up to 600 then burnish and 0000 steel wool the piece. I apply paste wax with the steel wool also. This allows the wax to go on more evenly as the steel wool holds onto the wax better than a paper towel does. I crank up the speed and let the piece just run for a bit until the wax is ready for buffing. Grab a clean paper towel and apply moderate pressure to build up some heat and really make the piece shine.

Now on to the finial. Start of with the piece between centers or in the chuck and turn a tennon for a chucking point. Looking back on it, I could have turned the finial without having to rechuck it.
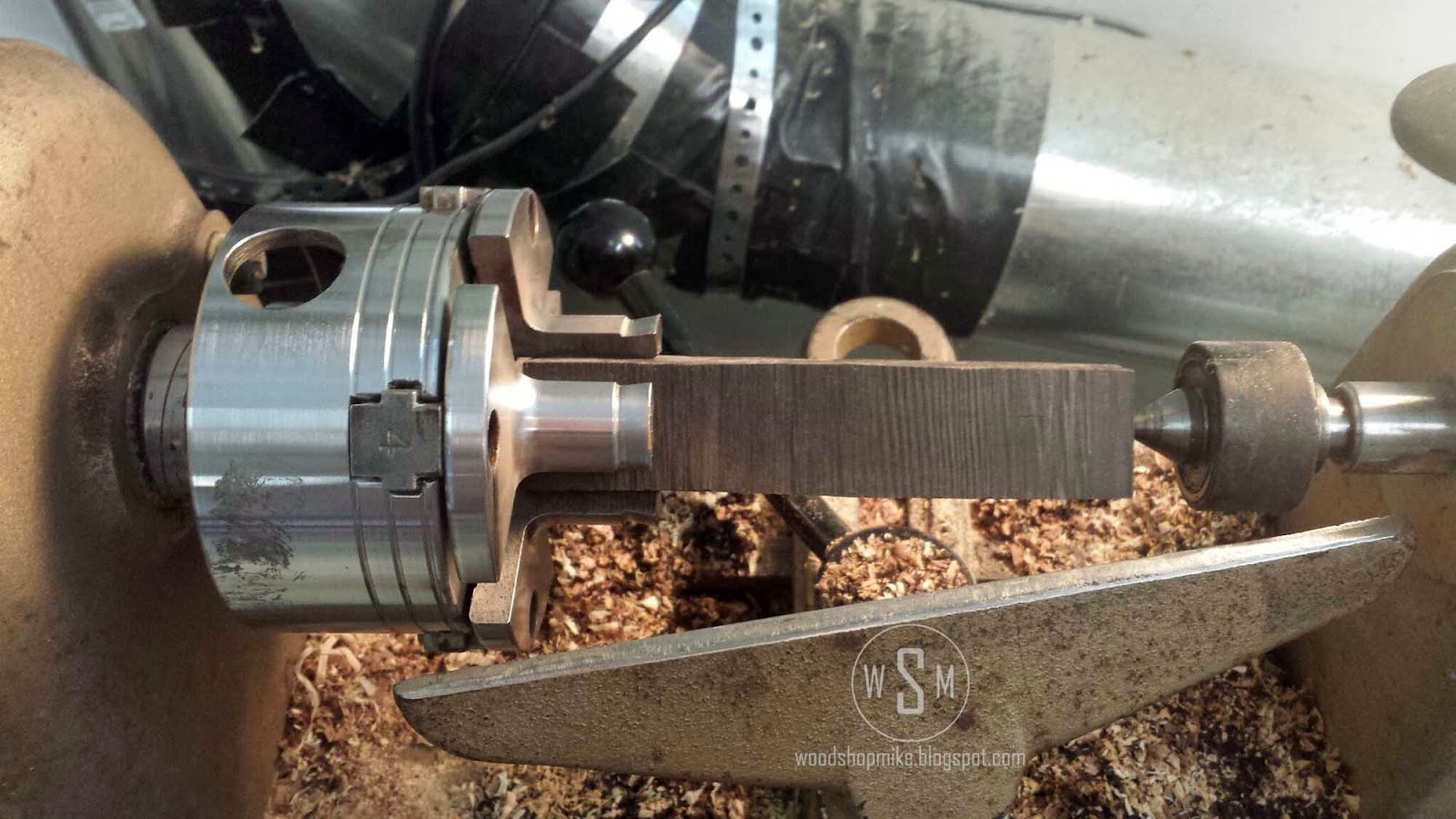
The reason I did turn a tennon and rechuck the piece is so that I could accurately put the piece back in the chuck if I happened to "dig in" and cause the piece to no longer run true. You are less likely to do this if the piece is held as securely as possible, which a tennon affords you.
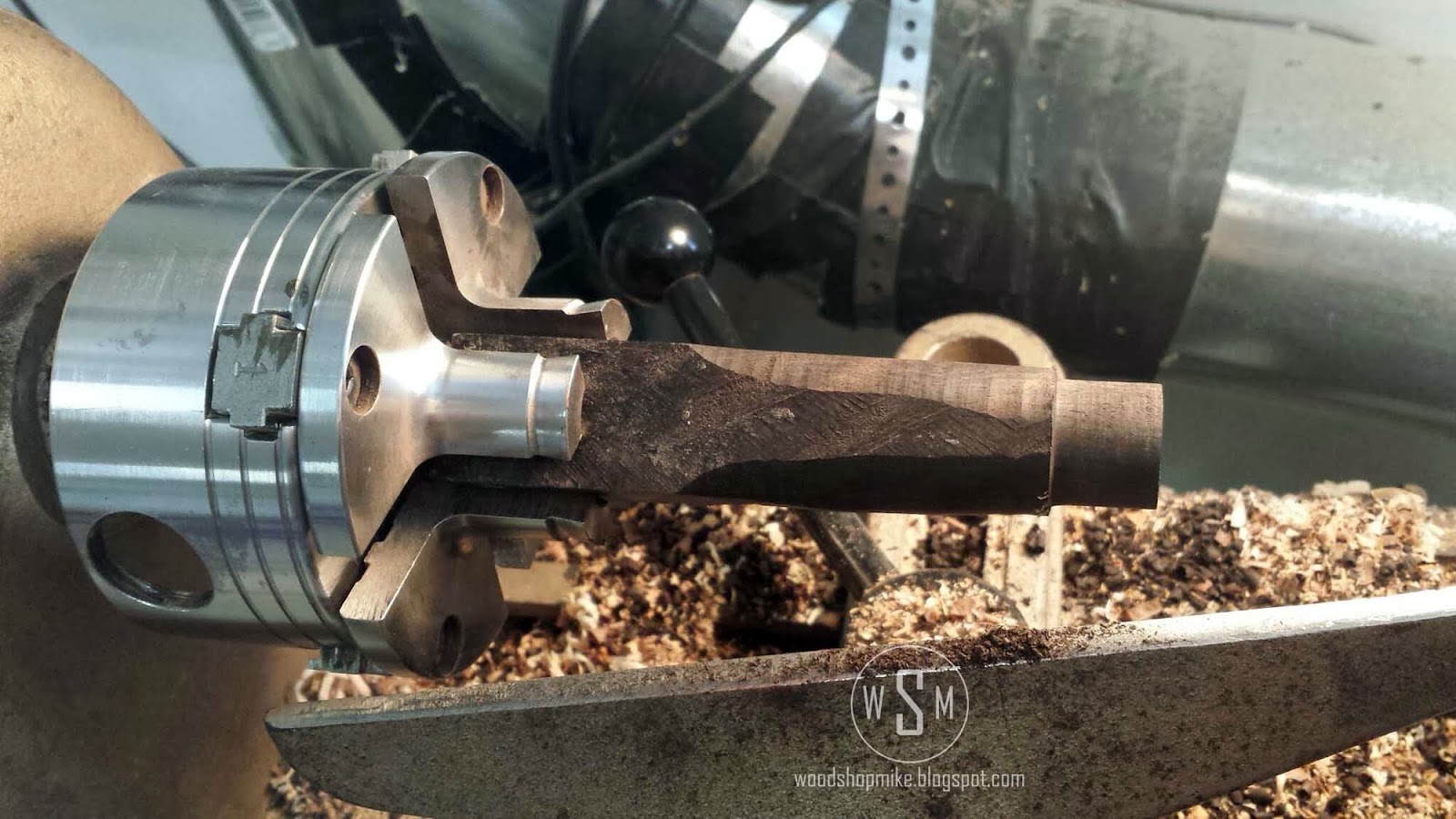
src="https://blogger.googleusercontent.com/img/b/R29vZ2xl/AVvXsEjNPIfG_V1slvNxcC8HLlc2Z6EbGPeFf5eLAvdC54Ko8Aa5t7TuZqzy2CngUFznGMxXtc5bnimW5ieLnUc_fGQRdMvlDnsM4gVFpnNwbWUnug2jKOhW_SeMnAhtpixnrHatONsvlj9S76o/s1600/20140301_104627+copy.jpg" title="Finial Blank Reversed" width="200">
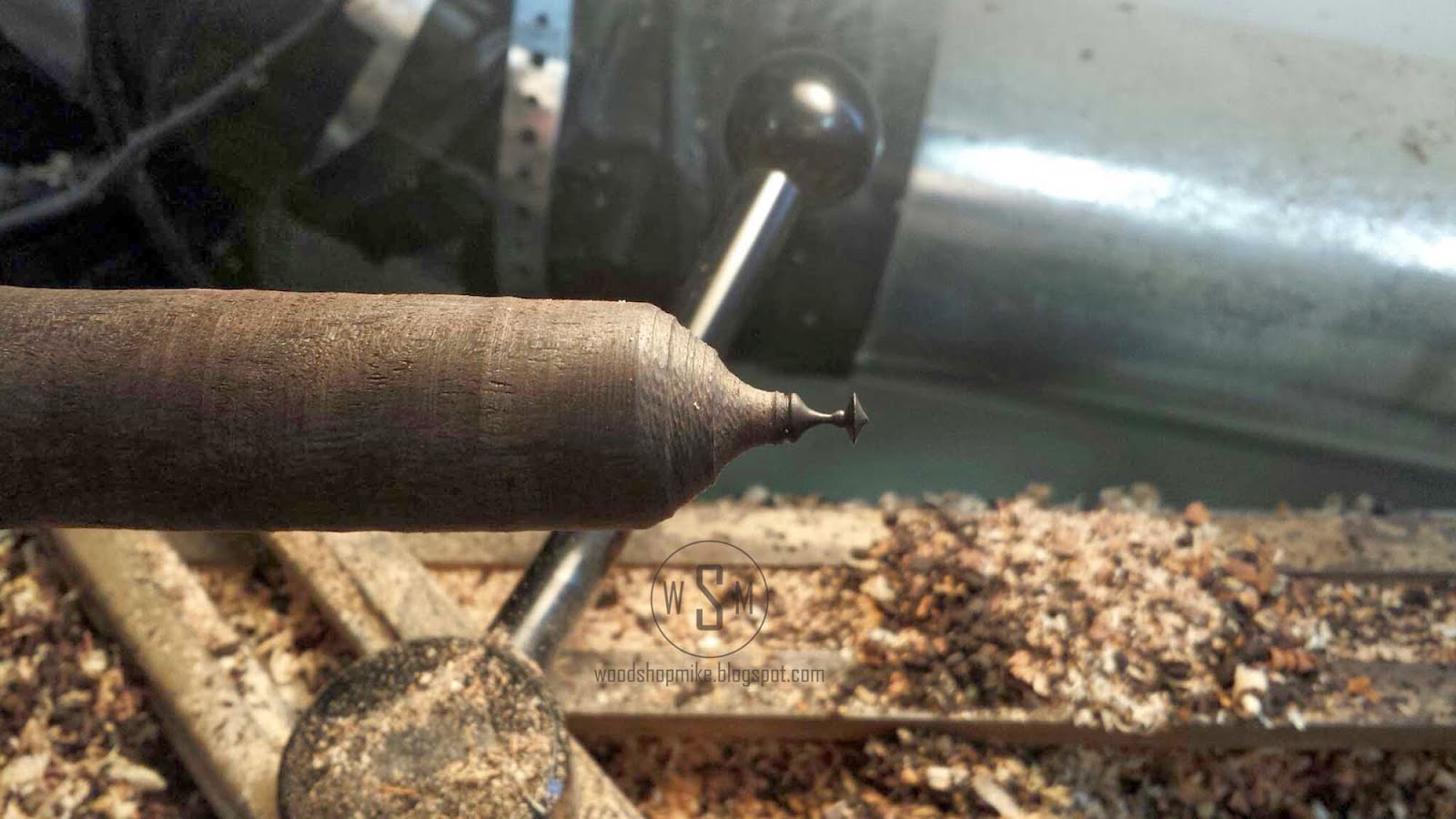
And then this happens. I usually just mutter under my breathe when I screw something up, but not this time... Well just leave it at that. If nothing else, I have a nice start to a spire, right?

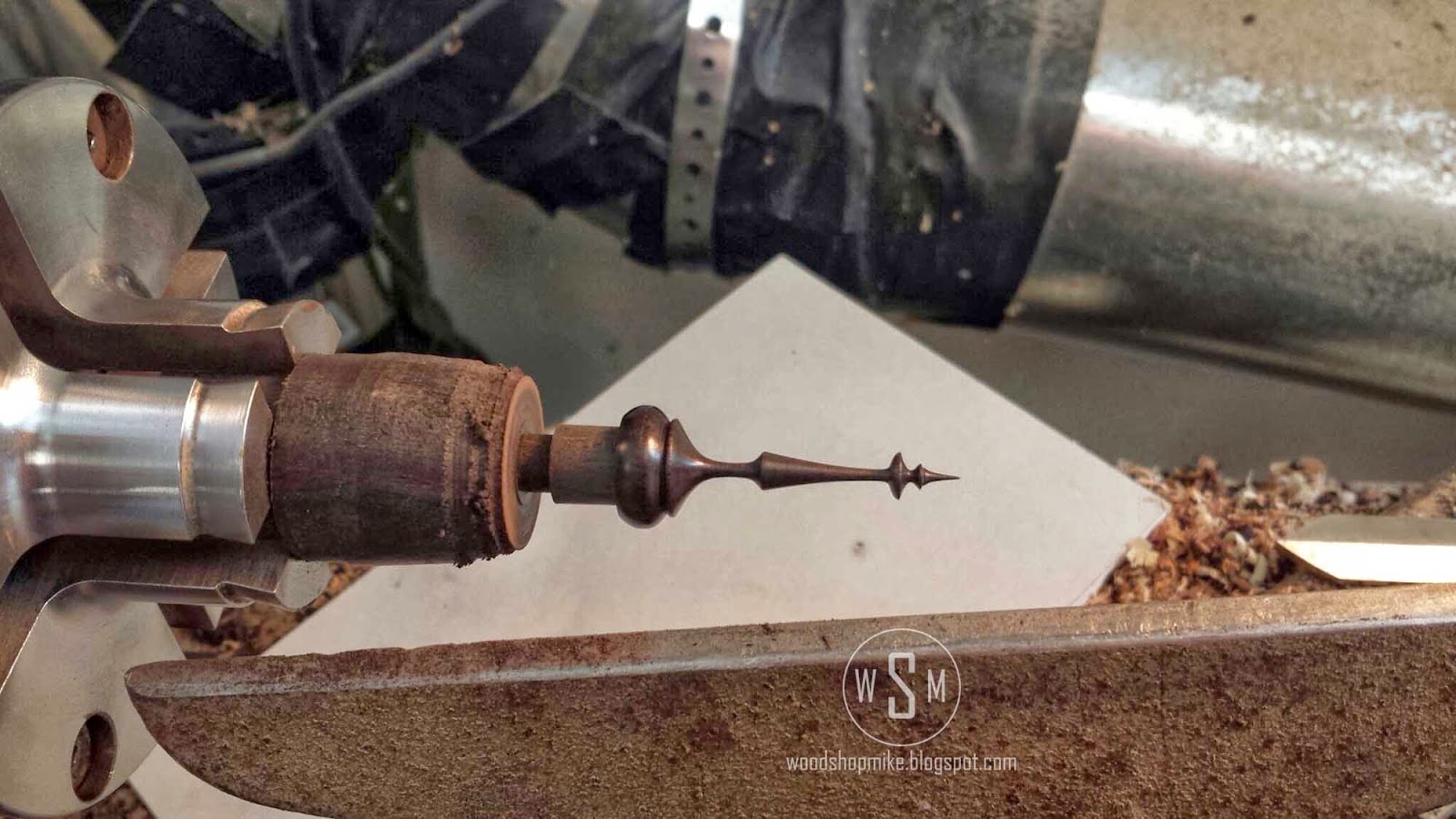
With the tailstock removed, I begin to shape my finial. When turning finials, it is imperative that you start at the end farthest from the headstock and work your way towards the headstock (right to left). I like to design while at the lathe most of the time, and was really pleased with the shape I was creating. I do have a problem though. I start to get really excited about finishing the rest of the piece sometimes...
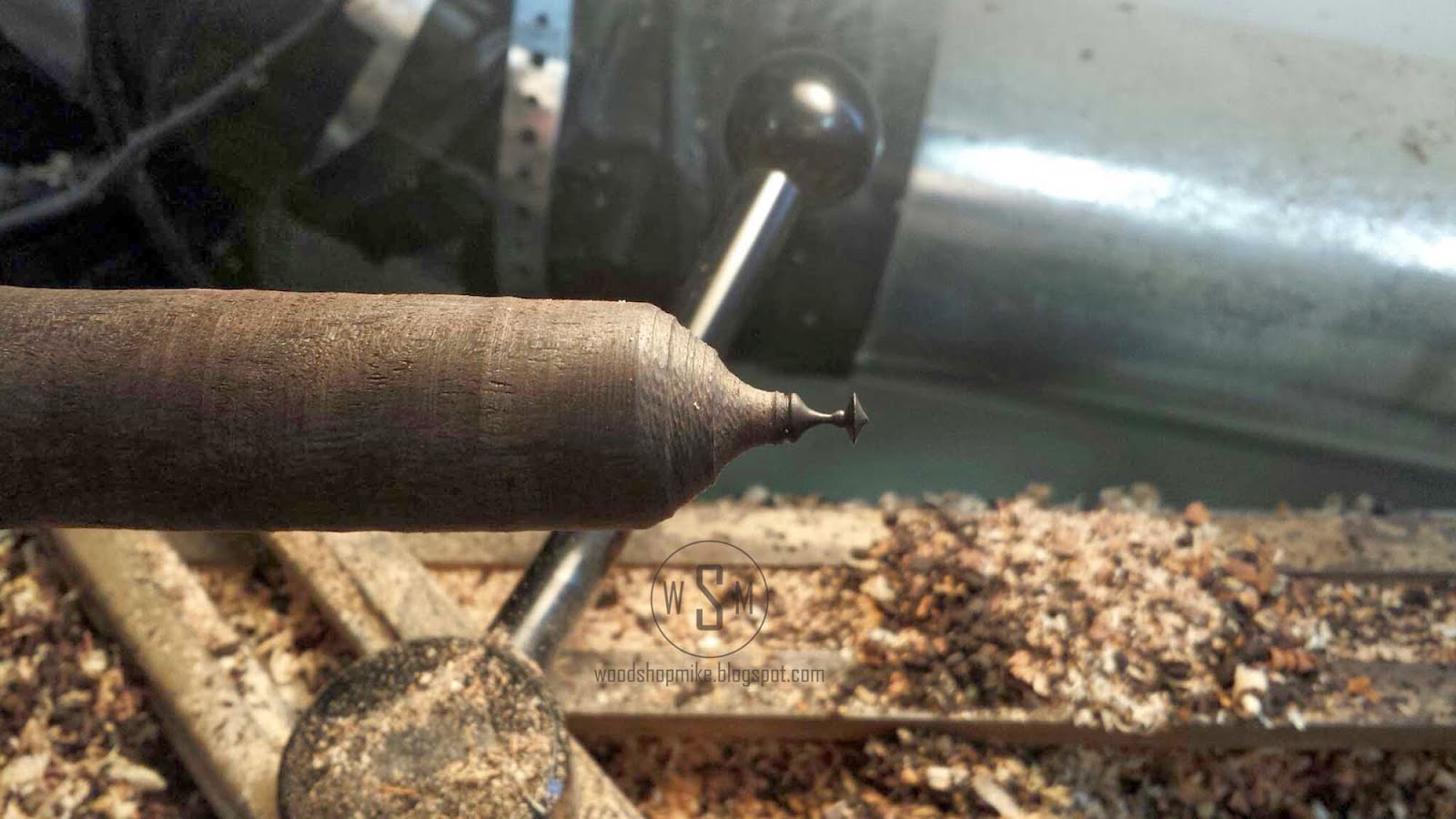

I decided to not take process pictures while making this finial because, well you saw what happened to the last one right? A camcorder would have been helpful here, but these are the basics.
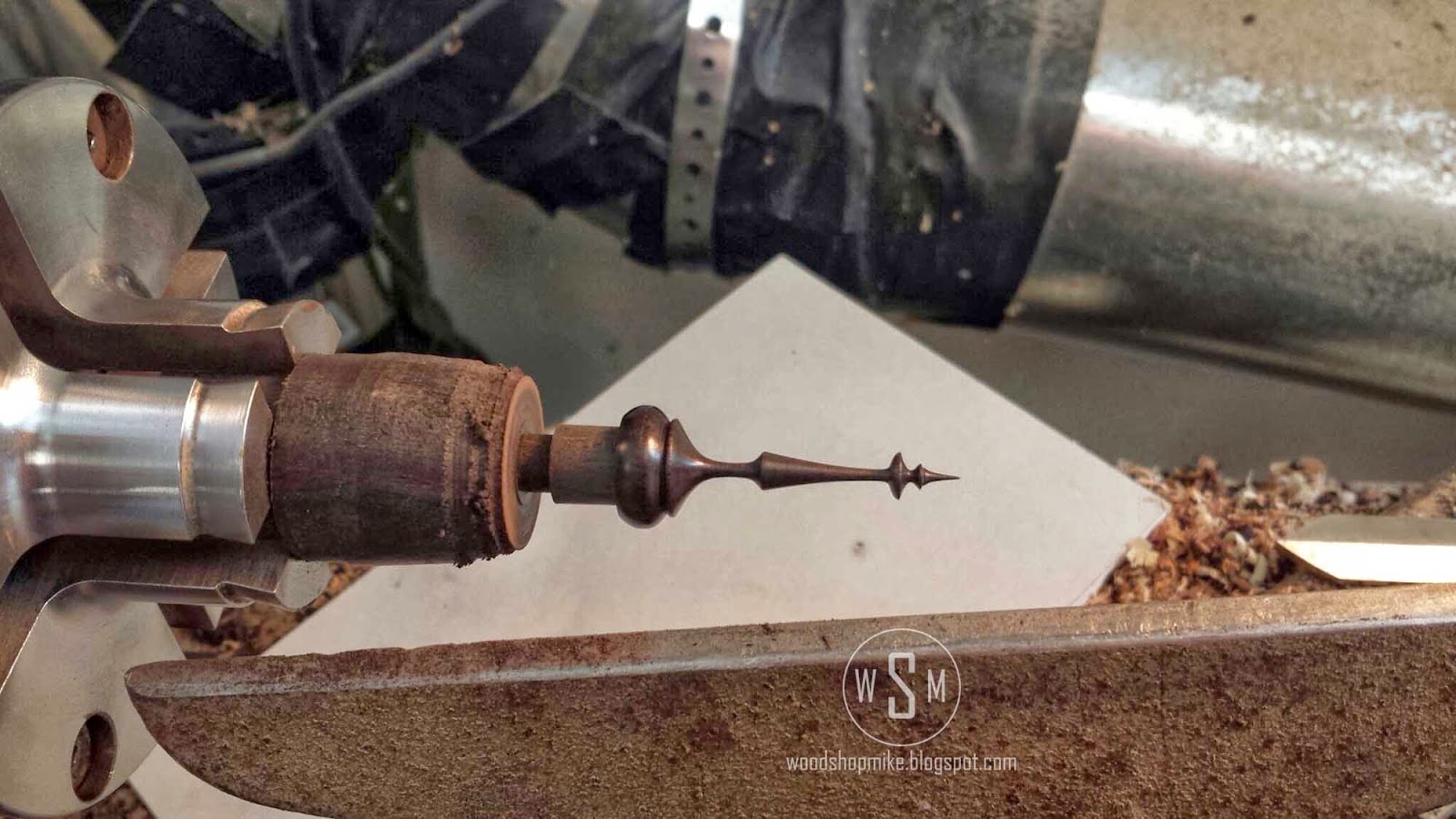
As I previously mentioned, work from right to left and completely finish one section before progressing closer to the headstock.
I use a 3/8th spindle gouge that has the wings ground back like an Irish grind and I shape a 1/8" nose on the end. The cuts I perform in the process of making finials are a pull cut (similar to bowl gouge), a push cut, and a planning cut.
When cutting with the nose of the tool (push), point the tool in the direction of the cut you want to make and "rub" the bevel. Swinging the end of the handle at differing speeds while advancing the the cutting edge will allow you to create a range of arcs.
For cutting small details, start with the gouge in the neutral position (flute closed) and just push the tip of the tool into the wood. This presentation of the cutting edge will prevent the tool from skating left or right. From this same entry method, one can make coves by opening the flute as you advance the tool.
I mainly reserve the pull cut for removing wood as I work towards the headstock. With the flute opened to about 45° to the left, start on the right side of your cut (not touching wood) and steadily advance the tool to the left into your stock. Just reverse the flute to the right and feed to the right to cut in the other direction. Maybe that was obvious, but maybe not...
Finally for the planning cut. I use this technique to take light cuts and blend long tapers or curves on the long narrow section of a finial. The flute of the gouge is mostly closed with the tool angled at about 30° up and down. I generally perform this cut from left to right. In this orientation, the tip of the tool is pointing up and to the left, while the handle is pointed down and to the right. With light pressure, glide the wing of the gouge along the wood. This will produce thin curly shavings and is a great way to finalize a subtle taper or curve to a finial.
For really small details, I use a skew chisel that is turned on its side with the point side against the tool rest. The lightest touch is all you need to add a crisp detail to your corners. Sometimes, Ill also use a utility knife for these details.
If I totally lost you while describing my process, there are excellent videos on YouTube for turning finials. Id highly recommend checking out Cindy Drozdas videos, such as this one.
Thanks for reading, guys. Ill have another post soon showing the assembly photos and the final product. As always, feel free to ask any questions you may have.
0 komentar:
Posting Komentar