Need another option for reverse turning? A vacuum chuck could be your answer. Yes, there are other methods of reverse turning, but vacuum chucking allows you to hold natural edge pieces with ease. The objects that can be held by vacuum chucking are endless and the best part is that its easily modified!The following will spare you the learning curve I had and hopefully get you on your way quickly. My lathe has a hollow spindle with a few cross-drilled holes. This forced me to use a through spindle vacuum adapter instead of something like the Oneway Rotary Adapter.
If you are like me, youve spent a great deal of time studying online articles learning how to accomplish the task at hand. Many designs rely on using a double sealed ball bearing as a component to be a vacuum seal. I was skeptical of this, but moved forward in spite of my doubts.
For this system, you will need to buy or make an adapter for each side of your lathe. One will fit on the outboard side and the other will match the morse taper of your spindle. You will need two ball bearings. I used a R10 and 6000 series bearings. I would recommend double sealed bearings simply because of the dust that will be present . The main aspect that drives bearing selection for this purpose is the size of pipe fittings you will use. I had the R10 bearing on hand, so I had to use a 3/8 NPT fitting to adapt to this bearing.
In addition to bearings, you will need:
- material for your spindle adapters
- an assortment of pipe fittings
- all thread lamp tube (3/8" OD, 1/8-27 thread)
- valve rated for vacuum
- vacuum pump (well geez, I wouldnt have thought of that)
- filter for your pump
- vacuum gauge
- tubing (size of pipe fittings)
- pipe tape/pipe dope
- epoxy
- a bleeder valve is nice but not a must have
- a muffler for the vacuum pump
- electrical switch
- wire nut
- pliers and wire strippers
- wranches (wrenches for those of you not from the south)
- someone else to do all the work for you! (optional)
So, once youve assembled all of your loot, it may look something like this.
I started off by making the spindle adapter for the outboard side of my lathe. I used Delrin for this piece because it is not porous, can be shaped by hand with wood turning chisels, and it was available. Good reasons, I think. The downside to Delrin is that its terribly difficult to permanently bond something to it.
The criteria for this part are as follows:- needs to fit onto lathe spindle without too much slop
- hold bearing with slip/press fit
- allows lamp rod to pass through it and clamp on an internal step
This sketch describes how this part works in the original design.
Here are the process photos of making the outboard side spindle adapter.
 | Rough turning spindle adapter |
|  | Ball bearing recess |
|  | Flip it! |
|
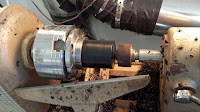 | O.D. profiling |
|  | Sized to fit out board spindle |
| 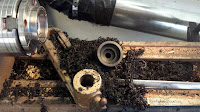 | Finished bearing side of adapter |
|
Now, lets move on to the inboard spindle adapter. For this item you need to:- match taper of spindle
- allow lamp rod to pass through
- make a surface for nut and washer to lock lamp rod in place
Here are the process photos of making the inboard side spindle adapter.
 | Roughing inboard adapter |
| 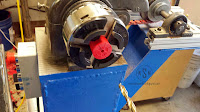 | Turning recess |
|
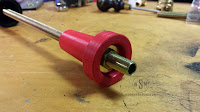 | Test fit |
|  | Reducing O.D. of adapter |
|
You may have noticed that I switched lathes while making this piece. I did this because my Nova G3 chuck doesnt have a large enough opening that I could push the spindle adapter into. Using the Vicmarc 120, I was able to hold the spindle adapter on the larger diameter and form a recess for the washer and nut to sit in.
Well, the spindle adapter is wrapped up... for now.
The next thing to move on to is pipe fitting! Oh what fun! I wanted to use push to connect (PTC) style fittings for this system so that I could easily adapt the vacuum pump to be used for other applications in the shop. While PTC fittings are not the answer for this application, this blog is a journey and youre invested, so lets see how things go.
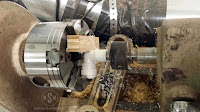 | Turning threads off fitting |
|  | Bearing, fitting, epoxy... |
|  | I didnt get epoxy on myself! |
|
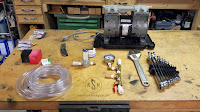 | Remaining parts for system |
|  | Manifold components |
|
Now with those parts all married, lets plug the suction end of the system and see what the vacuum gauge reads. This is where my disappointment began. For the pump to pull down more than 5" Hg, I had to push and hold the tubing into the PTC fittings... That will be hard to do while Im turning. In addition, the double sealed ball bearing was another leak. In an effort to remove as many potential leaks as possible, I rethought the design of my spindle adapter and replaced the PTC fittings with compression fittings.
I started by removing the plastic PTC fitting I had all too recently epoxied into the ball bearing. But first I needed to remove the ball bearing from the outboard spindle adapter. This was easily done by putting a screw driver inside the fitting (through the bearing) and hitting it with a hammer (plastic, no one wants a cracked screw driver) a few times. I then scuffed up the inner race of the bearing for the next fitting to be epoxied.
To remove the need for the seals of the ball bearing to hold vacuum, I changed the plumbing and affixed the lamp rod to the ball bearing with marine grade epoxy. This involved a few extra steps, which are shown with pictures below.
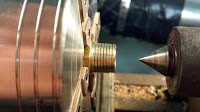 | Remove threads: 3/8 fitting |
|  | Cut off one side of 1/4 NPT |
|
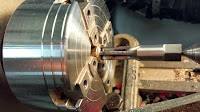 | Tap 1/4 NPT with 1/8-27 tap |
|  | All parts epoxied together |
|
Now that Ive affixed the lamp rod and bearing, I need a ball bearing for the other spindle adapter. By assembling the parts in this manner, I no longer need the "step" in the outboard spindle adapter. However, there is no need to remove it or remake the part.
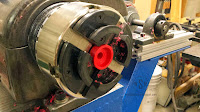 | Size adapter to fit bearing |
|  | Replacement compression fittings |
| 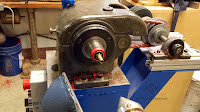 | Testing new configuration |
|
The last step is to attach the tubing from the pump to manifold and from the manifold to the spindle adapter.
 | Tube fitting for spindle adapter |
|  | Vacuum system! |
|  | Zip tie capacitor to keep it tidy |
|
I recommend testing your system for leaks before you use it for turning. A good way to do this is to plug or otherwise seal the open end of lamp rod, let the system pump down as far as it will go, and then valve off or turn off your pump to see what the leak rate is. This system isnt for a particle accelerator, so no need to go overboard. However, if the vacuum drops rapidly, you may want to look into it. A good way to find leaks is to mix up some soapy water and apply it to each of the connection points. You will see bubbles wherever there is a leak. Just give the fitting a bit more oomph and retest.
I will soon post about building vacuum chucks. I will be making my chucks completely from materials I have on hand and those commonly found at a big box hardware store! No face plate required for the method I will use. Once the holiday season is past, or once I catch up on my ornament orders (which ever is first), Ill make the vacuum chuck and finish off a platter!
Thanks for reading! As always, if you have any questions or comments, dont hesitate to contact me.
Related Posts by Categories
0 komentar:
Posting Komentar